
From raw aluminum to raw thrills
Modern aluminum fishing boats are incredibly sophisticated machines. Hulls utilize complex bends and curves that tame rough water and deliver a soft, dry ride, while interiors are made to combine durability, comfort and practicality. The end result is a sporty, versatile and durable boat that integrates the latest electronics, high-end live well systems, rod storage and more into an easy to maintain and affordable package.
The good folks at Smoker Craft Inc. invited us behind the scenes to see how aluminum fishing boats are made. Based in New Paris, Indiana, Smoker Craft is the parent company to the Smoker Craft, Starcraft and Starweld fishing boat brands. They’ve been building aluminum boats since 1903, and in that time they’ve refined the process to the remarkable mix of art and science that it is today. So let’s have a look at how modern aluminum fishing boats are created.
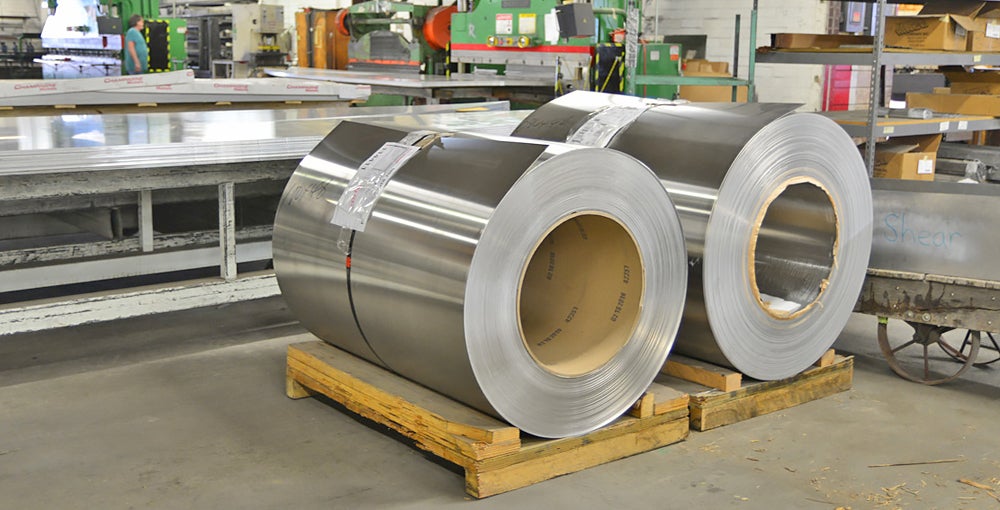
Rolls of sheet aluminum arrive fresh from the mill.
Whether they’re riveted or welded, all aluminum fishing boats begin life as massive, heavy rolls of raw aluminum plate that can weigh more than three tons. These massive rolls provide the aluminum plates of different thicknesses and textures, which are used to create the hull and other major components.
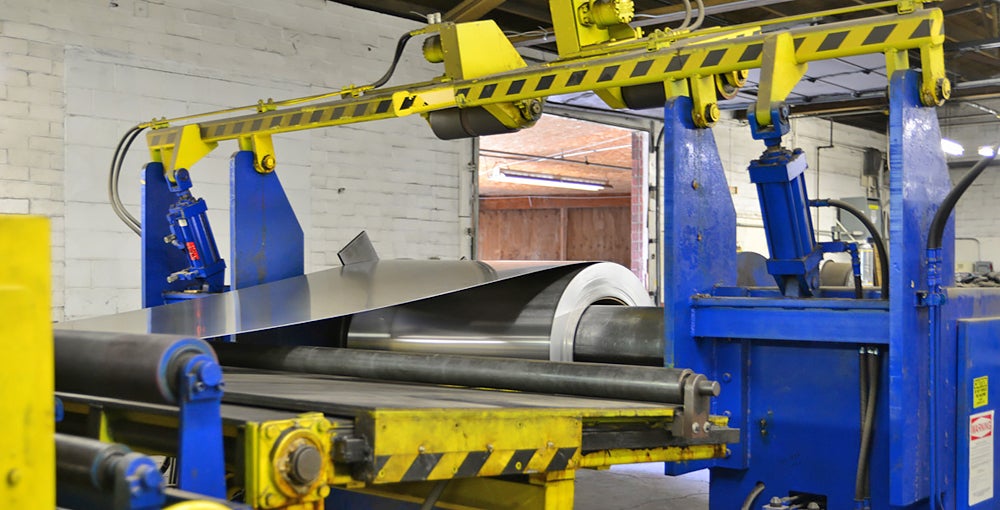
Smoker Craft’s decoiler in action.
The first step in turning rolls of aluminum into boats is to run the metal through a decoiling machine, which straightens the aluminum into flat sheets which are cut to length. Pieces used for hulls are cut to a little more than the full length of the finished boat, while pieces used for interior parts are shorter.
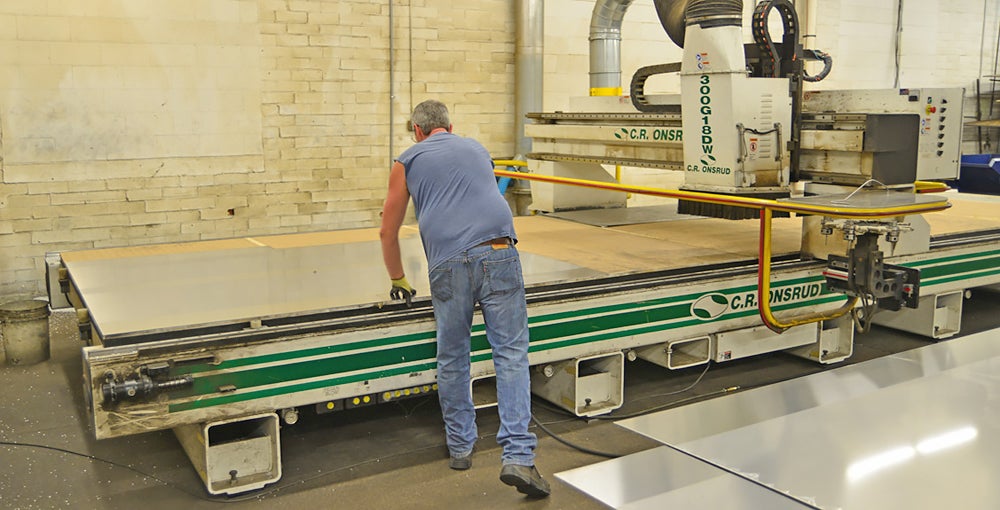
Flat aluminum sheets are next cut into parts using a CNC laser router that delivers precise cuts, minimal waste, and no sharp edges.
The flat plates then move to a cutting room, where sophisticated CNC laser routers cut the flat blanks into carefully shaped pieces which will form the hull bottom, the side gunnels, the transom, and countless other components. The laser router allows incredibly precise cuts that reduce the chance of sharp edges and the amount of finishing work that would otherwise be required later down the assembly process. It also allows multiple components to be cut simultaneously from the same aluminum sheet to reduce waste.
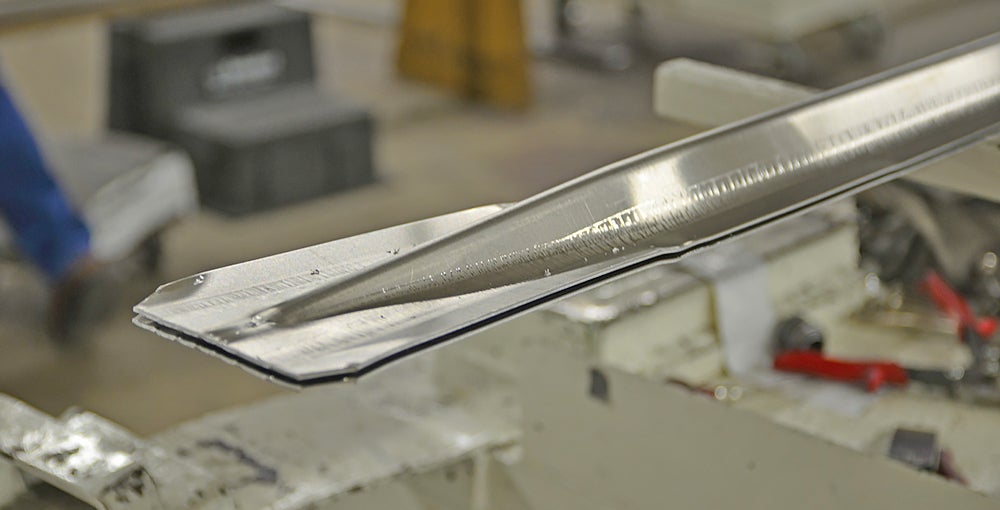
Ribs, spray rails and other formed parts are cut from narrower coils of aluminum on a separate machine.
While this takes place, another set of decoiling machines in another portion of the plant flatten and cut much narrower rolls of aluminum, which are formed into components like ribs and spray rails.
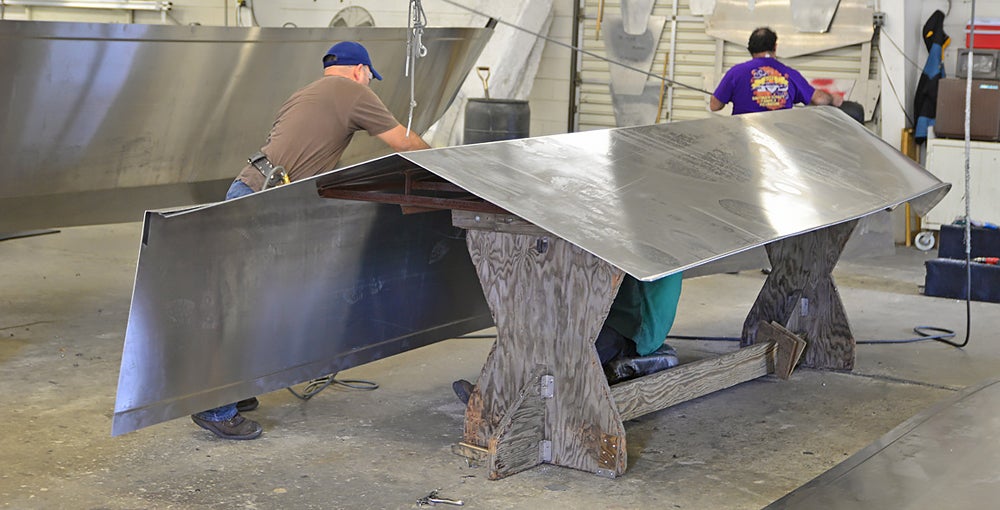
Special jigs support the hull bottom while the gunnels are attached.
The process of building a fishing boat starts when the heavy aluminum hull plates are loaded onto a jig, which secures the plates while skilled workers then attach the gunnels.
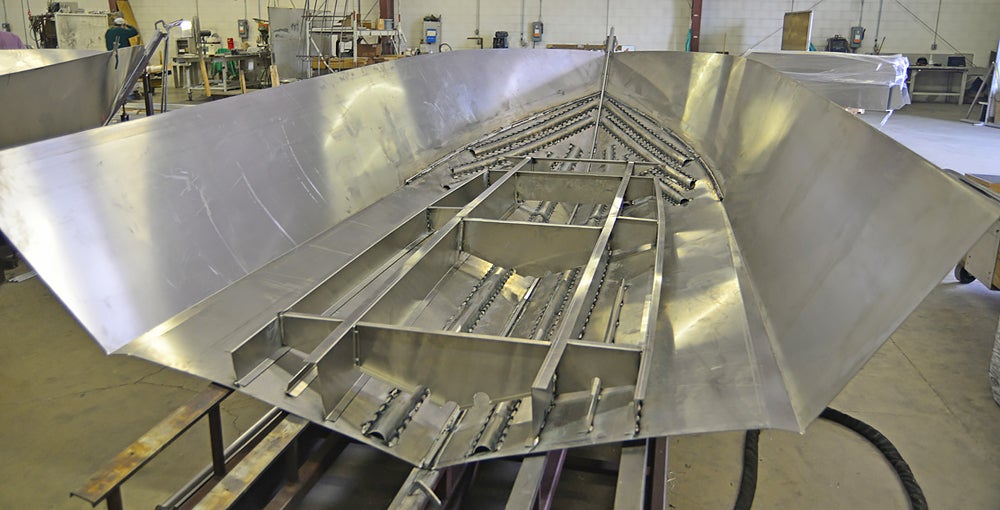
Internal frames are added next. The exact configuration varies by model.
Internal bracing and frames are then added to the inside of the hull to provide strength and torsional rigidity. Smoker Craft uses a variety of different internal bracing arrangements that are specific to the boat model being produced, for optimal strength.
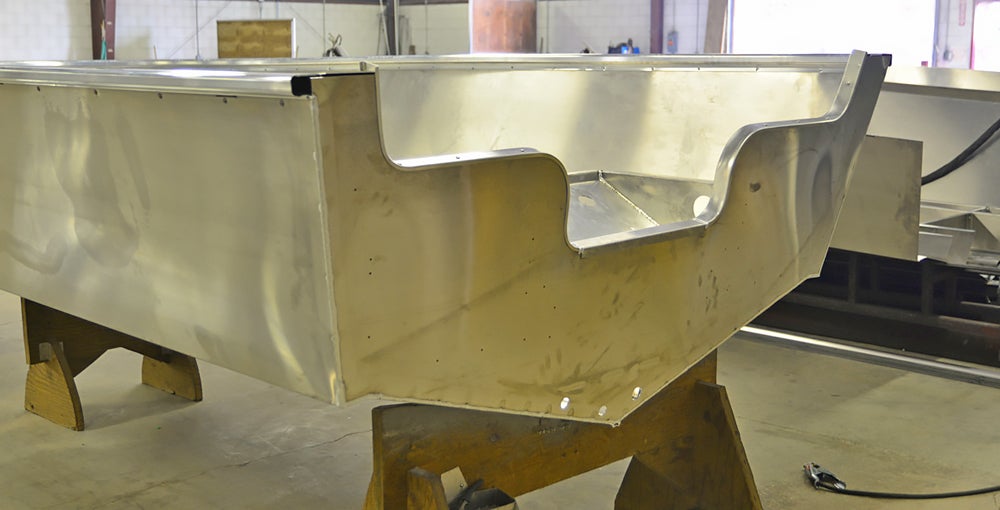
Now it’s starting to look like a boat!
Once the internal frame is in place. the next step is to install the transom. Depending on the specific boat model, the hull and transom assembly can be either welded or riveted.
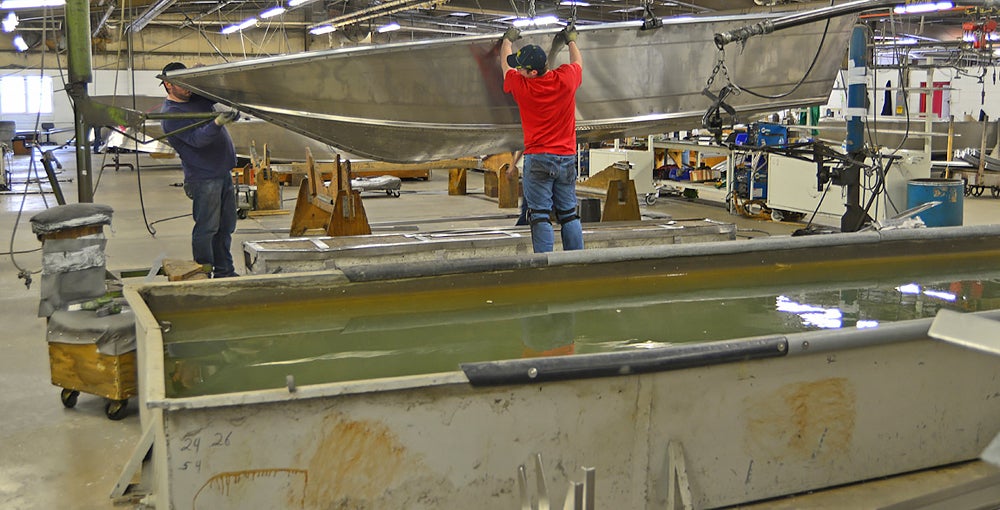
Every boat that Smoker Craft makes is hand-tested in water tanks to guarantee it is water-tight.
Once the outer hull structure is complete, it goes into a water tank for testing. Two technicians climb inside the hull and check the boat for any sign of leaks, misaligned rivets, faulty welds or any other potential defects.
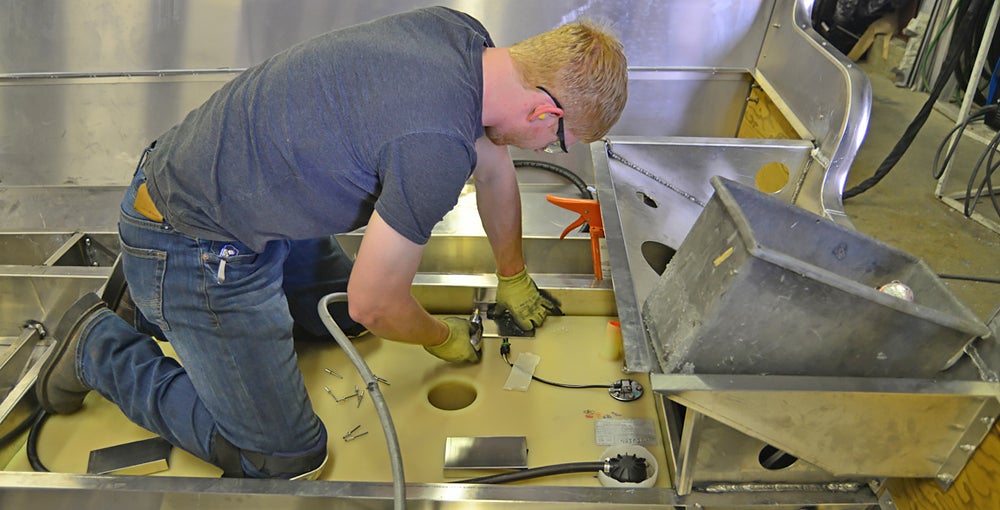
Sub-floor assemblies come next, including fuel tanks, wiring and plumbing for live wells.
Once the hull is certified as water-tight, work can begin on installing interior components that sit under the floor, like built-in fuel tanks, live wells, bilge pumps and electrical conduits.
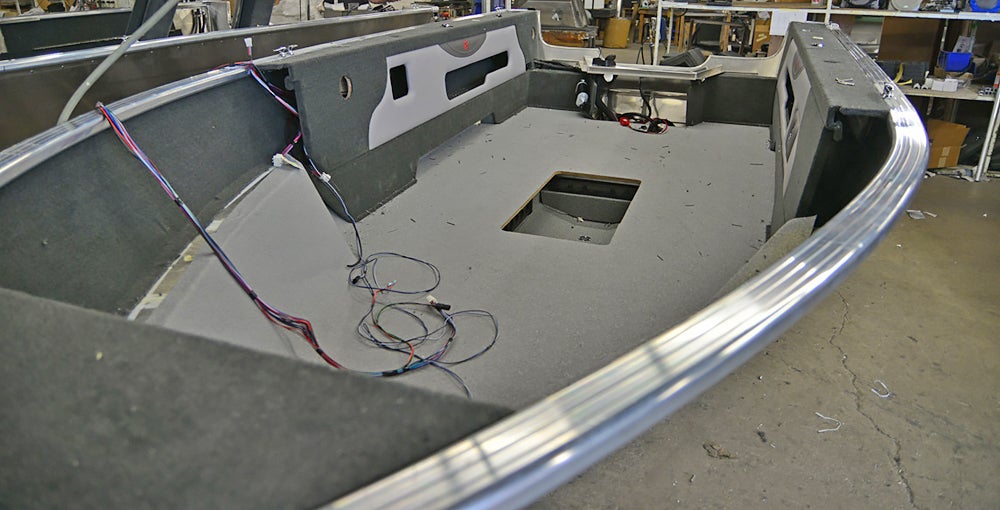
Expandable foam flotation is then injected under the floor in order to fill every possible cavity, before floor coverings and interior walls are installed.
Next comes the floor itself, and now the boat really begins to take shape. Once the floor is in place, the boat is filled with foam flotation, which is injected into the substructure through special access holes. The foam expands as it cures, filling any gaps under the floor and unifying the structure into a single, solid unit. The expanding foam also eliminates any places where rain could collect under the floor and form mold. The deck is given a final sanding to get rid of any bits of dried foam extending above the access holes, and then floor coverings and side panels are installed.
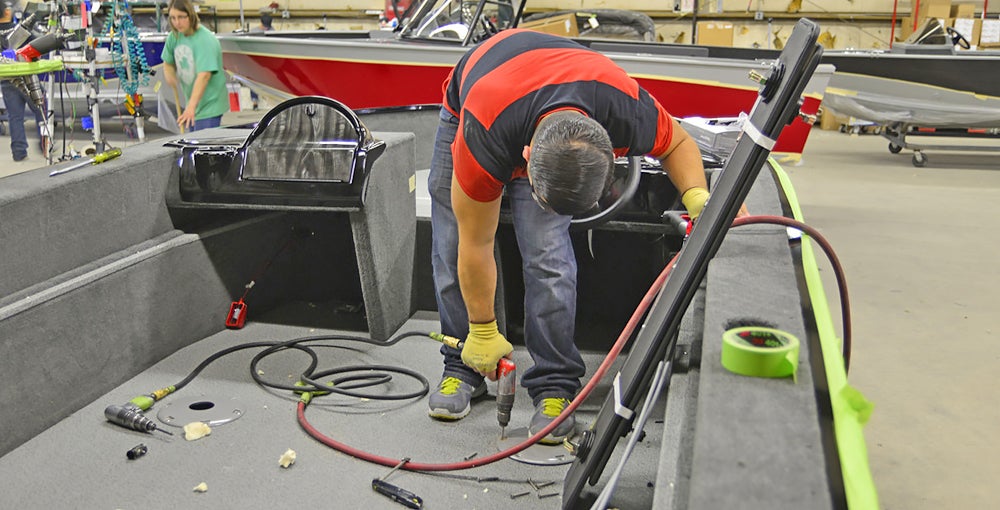
Next come interior assemblies like consoles, bases for pedestal seats, and other equipment.
The boat comes together quickly now as major components like the helm console and the splash well, which have been pre-assembled elsewhere in the plant, are installed, along with the seat bases and other interior components.
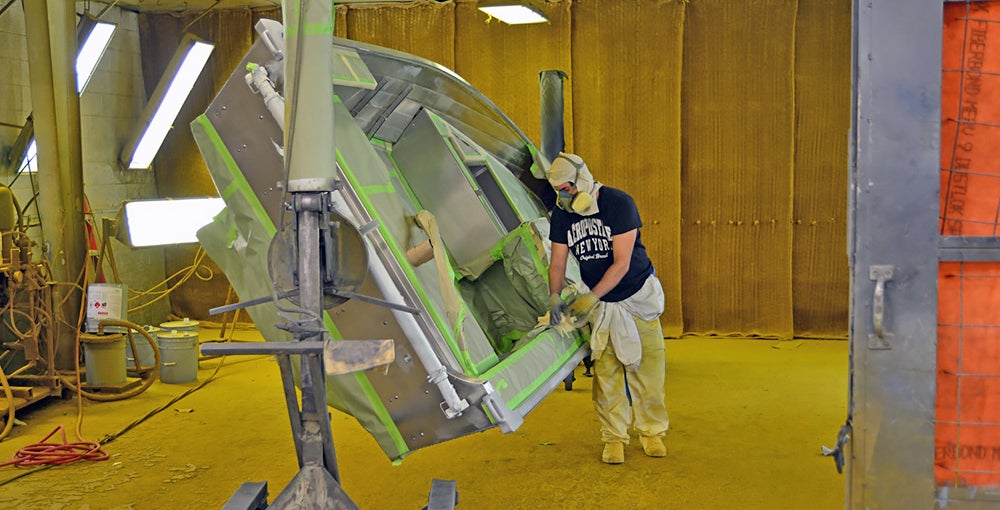
The boats are then thoroughly cleaned and masked off before heading first for the paint booth, and then to a drying oven that ensures a durable, baked-on finish.
At this stage the entire boat is thoroughly cleaned in preparation for painting. Working in a dust-free environment, dust, dirt, waxes and even fingerprints are carefully removed using a progressive range of cleansers until the boat is essentially sterile. Skilled workers then then begin the process of masking off the boat as required, including intricate taping work for what will become the final graphics. The masked boats then go into the spray booth where they receive a primer coat, followed by a series of tough, urethane color coats. After baking in an oven for a durable, smooth, hard finish, the boat emerges from the paint shop and the masking paper is carefully peeled away.
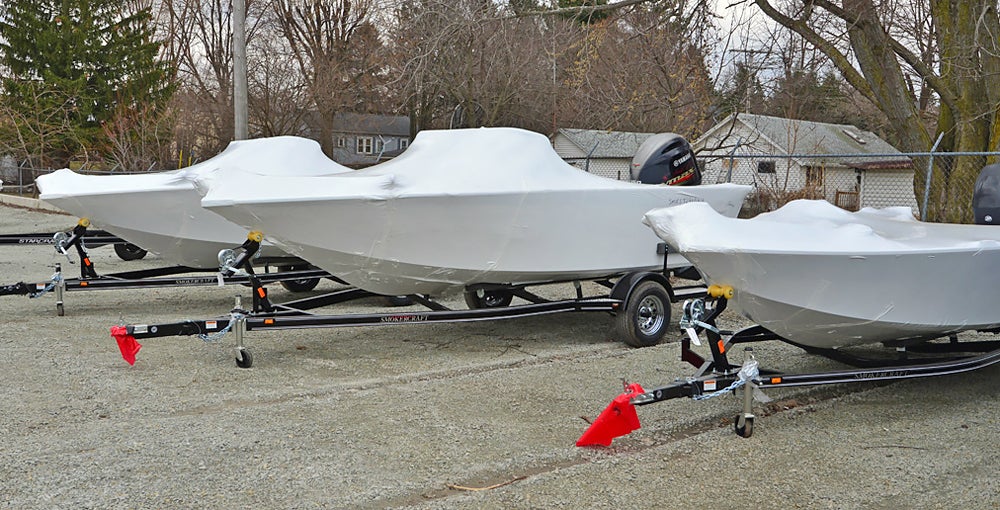
After adding final touches like windshields and pedestal seats, the boats are shrink-wrapped and shipped to waiting buyers.
Once boats come out of the oven the final components like steering wheels, outboard engines, windshields and pedestal-mount seats are installed. The boat is then ready to go! It’s carefully shrink-wrapped to protect it in transit, then loaded on one of the company’s nearly 30 trucks and shipped off to its new owner.
Talk about an interesting process! Thanks again to Smoker Craft for showing us the ropes, and for sharing a unique insight into how today’s aluminum fishing boats are made